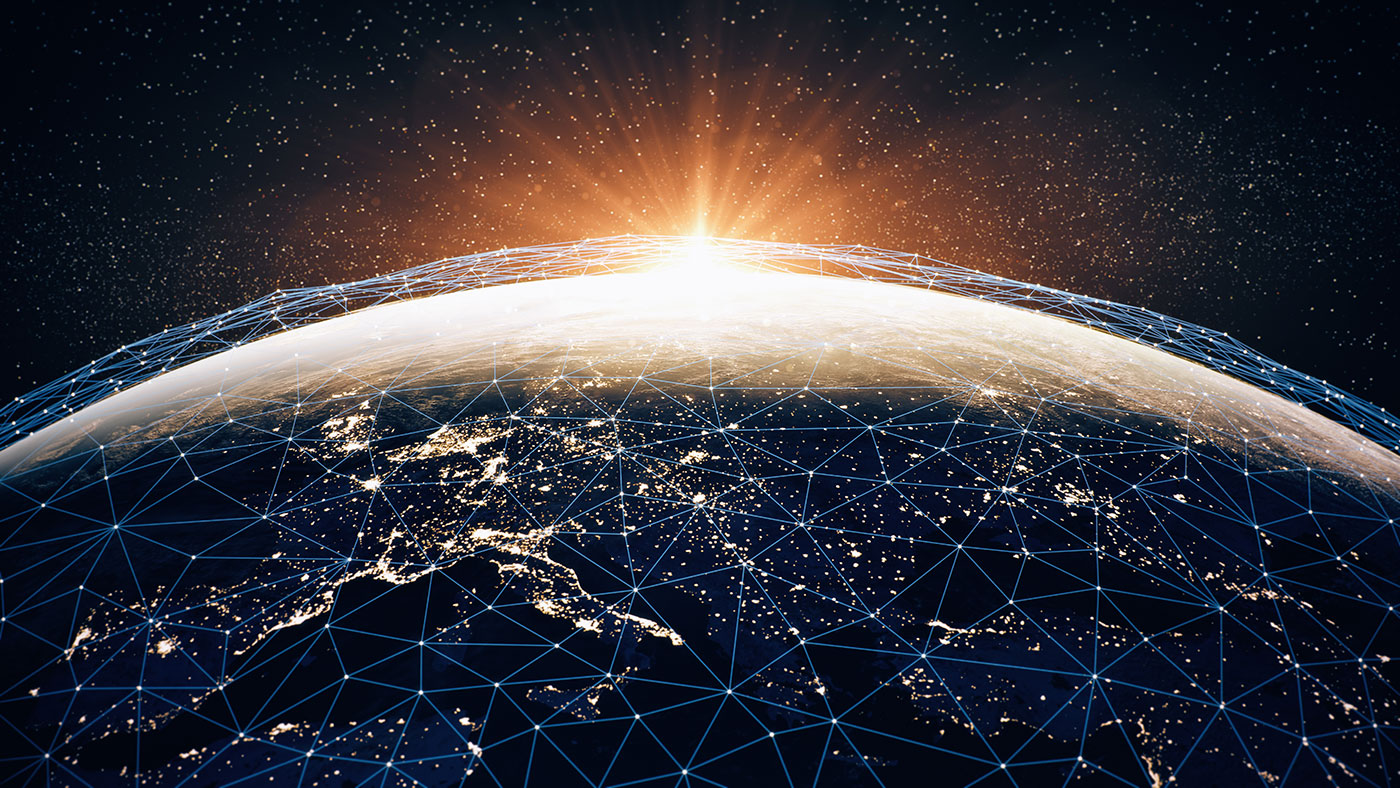
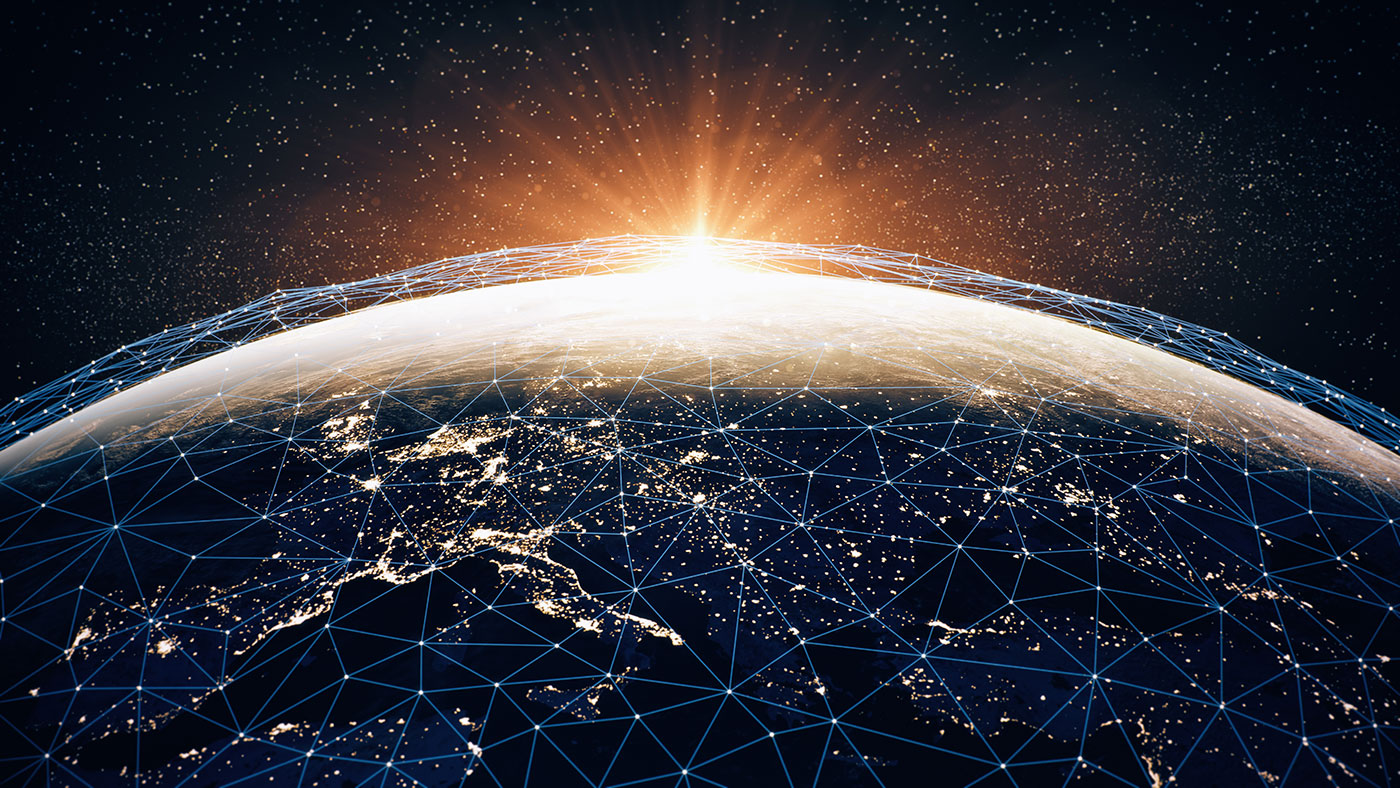
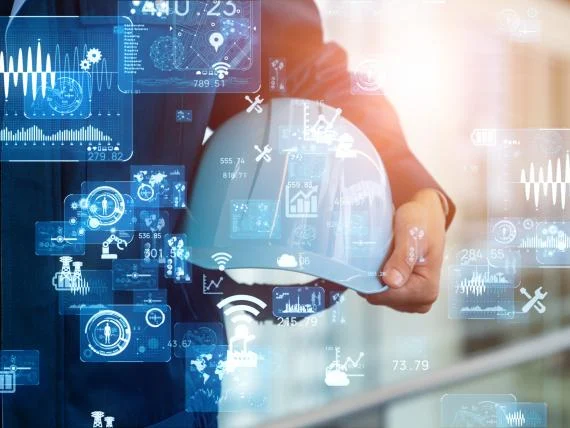
Imagine if you could not just monitor incidents, but predict them and prevent them using data – saving your organisation money and keeping your workforce healthy and safe… We’re working with academics and the construction industry to find an evidence base for using ‘leading indicators’ to prevent people from being harmed at work. Leading indicators are measures linked to the proactive, preventative things we can do to keep people safe. These can include things such as providing protective clothing to less obvious ones such as promoting healthy lifestyles and looking after mental health.
We hope this work will help avoid some of the accidents that happen in construction – a high-risk industry that still sees 40 fatal injuries to workers each year, 61,000 non-fatal injuries, 2.1 million working days lost due to work-related injuries or ill health and a total cost to the UK economy of around £1.2 billion each year.
Safety has come a long way through industry being open about what goes wrong, and learning lessons from accidents and incidents, statistics like this show there is a long way to go before harm is reduced to zero. The next step is to prevent things going wrong in the first place, according to Steven Naylor, the data scientist leading this project:
“If, by getting the construction industry to be more proactive in how they manage risks, we can achieve even a 5% reduction in these metrics, it would mean two lives saved every year, over 3,000 serious injuries and over 100,000 lost work days avoided and cost savings to the UK economy of the order of £50 million.”
Safety professionals in industry have understood the link between proactive measures and better safety outcomes for some time. But proving this with hard evidence has been elusive.
The ‘Leading Indicators’ project is a key part of our Discovering Safety programme. Steven explains: “Using leading indicators means being more proactive and understanding the processes that lead to things going wrong, not just reacting when they do. We’re making the case for developing safety processes based on what we do, rather than what we don’t.”
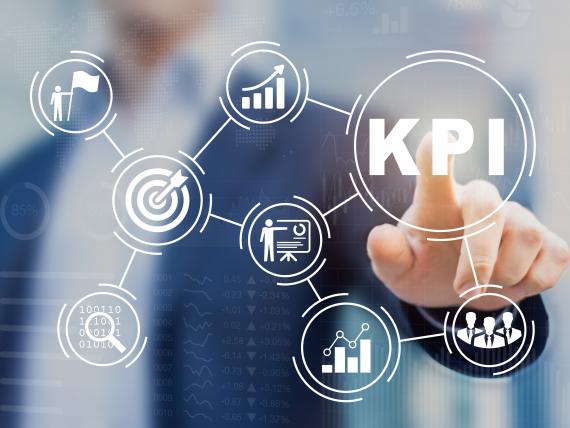
Rigorous collection of statistics on accidents, incidents and near misses is now standard, and drilling into this data can bring forth useful insights into root causes. Our Leading Indicators project goes further by using sophisticated software to show the causal link between positive interventions and better safety and wellbeing at work.
We are supporting the construction industry to gather data on the effectiveness of preventative measures such as training, communications and health and safety management practices – as well as the important ‘lagging indicators’ such as accident frequency rates and lost time injuries.
By measuring the number of times that things are done right, we hope to find and demonstrate the correlations between good practice and reducing harm. This evidence-based approach will allow employers to show their workforce the benefits of the positive measures they put in place.
The Leading Indicators project has three phases. Phase 1, in collaboration with the University of Manchester, started 18 months ago and focused on building an evidence base to use as a framework.
Phase 2 began in 2020 and involves testing the framework and seeing how to apply it. This means drawing on data held in the HSE’s vast repository of accident and incident reports, to find the evidence for the areas that are most in need of focus. Phase 2 is being carried out in partnership with international construction contractors Wood PLC.
The first part of Phase 2, recently completed, involved workshops with construction contractors from the UK and Ireland – such as BAM Nuttall, Multiplex, John Sisk, Blu-3 and Wood – to document the range of data practices currently being used by contractors.
“We sat down with the contractors to understand how projects are managed from day to day, and what the key challenges are,” Steven explained. “This was important as we need to make gathering this evidence feasible on a busy work site.”
Steven’s team is using not only readily available data but also data from the pre-construction stage of a project. This is more challenging to obtain but provides insights that will help the new, proactive processes work in the real-world, complex construction workplace, where the workforce comprises not only contractors, but client representatives, subcontractors and designers.
“One thing that’s becoming really evident is that lots can be done at the design and planning stages, before construction work begins,” says Steven.
Stage 3, planned for later in 2021, will help construction contractors make better use of the data they gather, using automated data-gathering tools such as text-mining and artificial intelligence. To help us do this, the contractors shared samples of routine health and safety data generated on their projects, such as incident reports, the findings of inspection and audit reports and project observations.
This data, along with data already held by HSE, is being used by the HSE and Wood project team as the basis for developing new analytic tools and techniques that industry can use on their own data in the future. We will then work towards getting this integrated into existing software.
“We’ll assess currently available software solutions to identify any gaps in capability and functionality, before developing solutions to address them,” said Steven.
Having more proactive and more data-driven safety management processes will mean that contractors have:
- Measures of health and safety performance available in real-time (or nearly)
- End-to-end processes that start with the raw data being generated and end with it being auto-collated and reported on
- Measures that are more directly linked to agreed actions, for example, documented risk hotspots triggering targeted inspections.
If you’d like to be part of this drive for more proactive safety that holds the promise of preventing avoidable death and injury and unnecessary cost to industry and the economy, contact discoveringsafety@hse.gov.uk.
Related Content