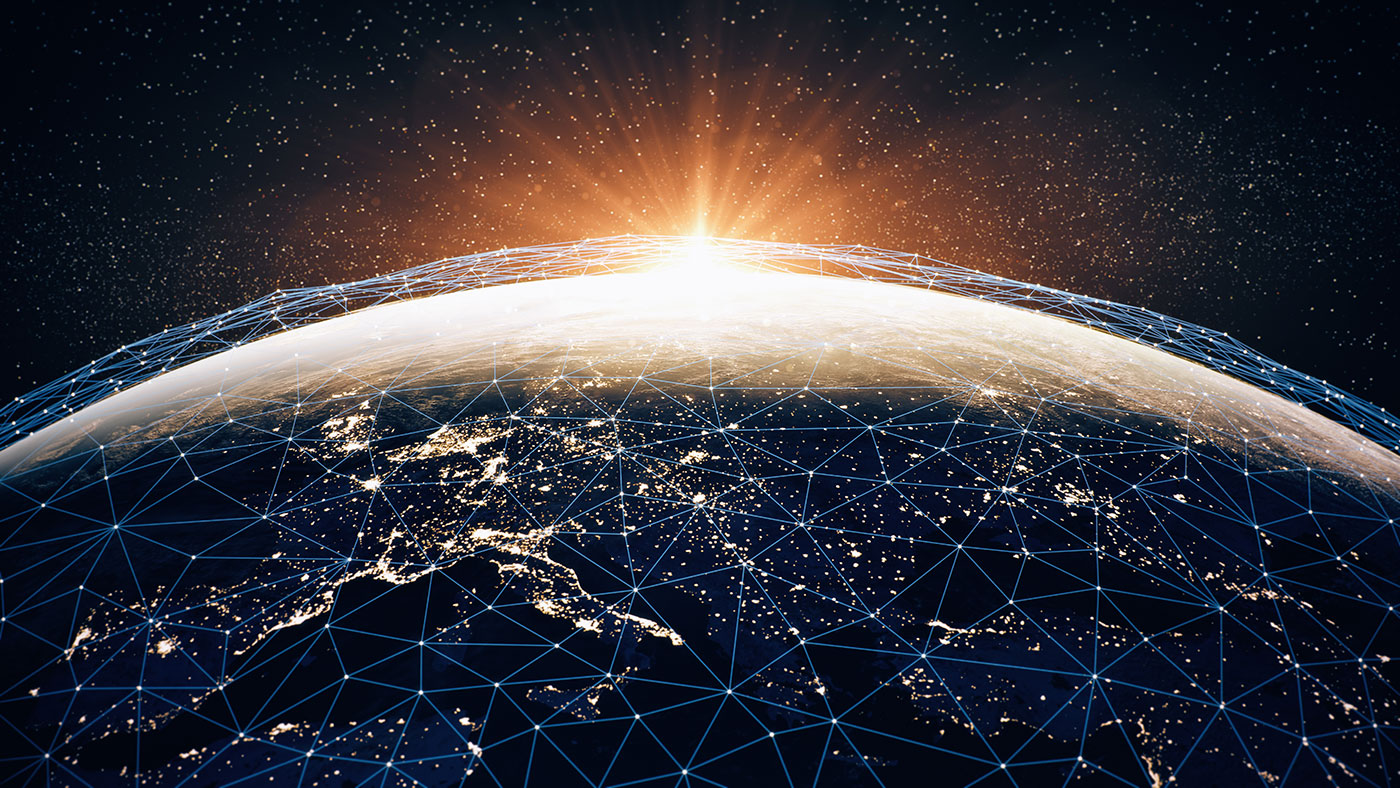
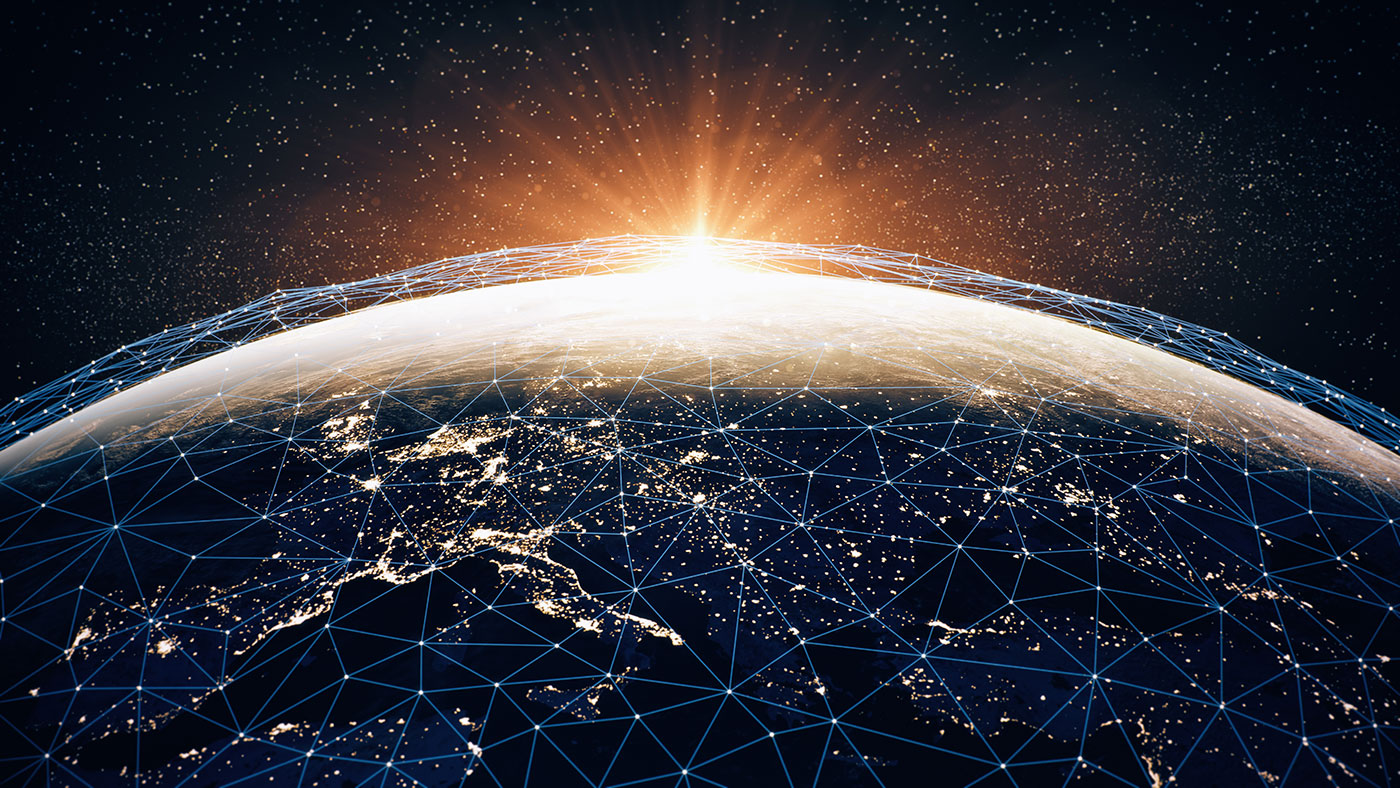
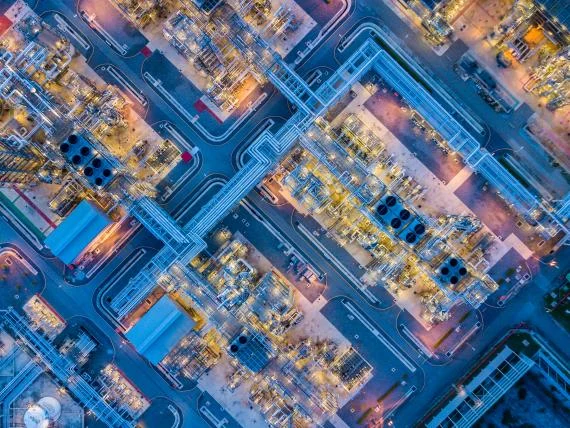
The fourth industrial revolution, often termed industry 4.0, the name given to the emergence in use of a suite of technologies, originally in manufacturing workplaces, but increasingly in other sectors also, is transforming how operational decisions are arrived at in industrial workplaces. The technologies in question, including smart sensors, wearable devices, mobile devices, robotics, artificial intelligence, advanced algorithms and data analytics, the industrial internet of things and cloud computing, are enabling detailed digital snapshots of operations to be generated and subsequently used to support and even completely automate operational decision-making.
The third industrial revolution was characterised by the widespread emergence of computer controlled systems and automation within workplaces. Industry 4.0 technologies introduce the concept of cyber physical systems (CPS’s), integrations of complex physical machinery, networked sensors and computer software, which are able to self-monitor and then adapt their functioning to optimise performance based on the current prevailing operational environment.
A key component of CPS’s is the increased level of connectivity across constituent devices and industrial processes. Such connectivity is made possible in large part through the use of miniaturised computing devices and sensors . The internet serves as the channel through which such devices are connected and information flows between. As the internet becomes faster (a step change in performance is expected following the future rollout of 5G mobile internet) , the capacity to link hundreds and even thousands of devices with one another, stream data efficiently and use it near time and real time, will only grow.
CPS’s are transforming the interaction between humans, equipment and industrial processes in workplaces. Such transformations are increasingly extending to how health and safety is practiced in workplaces and the general consensus of opinion amongst health and safety practitioners is that this is only likely to gather pace. In fact in some workplaces, industry 4.0 technologies are being used directly for the purposes of better managing health and safety risks (use of wearable devices to monitor the locations of workers relative to workplace hazards, or sensors on safety critical plant to inform maintenance and servicing schedules, for example). More commonly however, they are being used more for optimising operations and delivering improvements in process efficiency, but in doing so, it is evident that new health and safety risks have the potential to be introduced into workplaces, particularly in the event that unintended health and safety consequences result and in certain circumstances when they fail. The potential dual effects on health and safety, both positive and negative.
The rise in use of industry 4.0 technologies also has the potential to place new demands on health and safety regulators in terms of their abilities to discharge their regulatory duties effectively. For example, the central responsibilities facing regulators of judging the extent to which specific health and safety risks are sufficiently well managed in workplaces, and investigating root causes when serious accidents happen, have the potential to be significantly impacted. However, future opportunities also exist for regulators to exploit the technologies to enhance how they regulate health and safety across workplaces. For example, it is conceivable that the technologies might be used in the future to facilitate the reporting of accidents to regulators, how workplace inspections and functional checks of safety critical equipment are undertaken, particularly in remote workplaces, how requirements for worker health surveillance are met, how regulatory enforcement activities are targeted and subsequently delivered and how industry guidance is shared.
Related Content